Future of Aerospace: Key Innovations Transforming the Industry
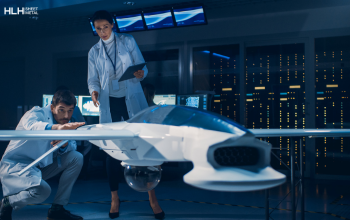
The aerospace industry has always been a leader in innovation. It pushes the limits of engineering, technology, and exploration. As we go further into the 21st century, the industry is changing quickly. This change is due to new materials, digital technology, and a greater focus on sustainability.
In this blog post, we will look at key innovations that are shaping the future of aerospace. Let's also discuss what these changes mean for the industry.
Advanced Materials in Aerospace: Revolutionizing Aircraft Design
One of the most significant advancements in aerospace fabrication is the development and use of advanced materials. Carbon-fiber composites, for example, are now a staple in modern aircraft construction. These materials offer exceptional strength-to-weight ratios, which translate to improved fuel efficiency and reduced operating costs.
Researchers are also looking into smart materials. These are substances that can change their properties based on environmental conditions. Imagine aircraft wings that can adapt their shape mid-flight to optimize aerodynamics. Such innovations could redefine the design and functionality of future airframes.
How Modern Materials Help the Aerospace Industry
Reducing Weight
One of the primary goals in aerospace manufacturing is to reduce the weight of aircraft. As lighter designs lead to better fuel efficiency and lower operating costs. Materials like carbon-fiber composites and aluminum alloys have revolutionized aircraft construction by offering high strength while significantly reducing weight.
Improving Passenger Comfort and Safety
Modern materials also contribute to enhancing passenger experiences. Lightweight composites can dampen cabin noise, while advanced polymers improve seat ergonomics and fire resistance. This ensures safety and comfort during flights.
Withstanding Harsh Conditions
Materials used for aerospace manufacturing must endure extreme temperatures, pressures, and environmental factors like UV radiation and corrosion. For instance, engineers prize titanium alloys for their ability to withstand harsh conditions while maintaining structural integrity.
Factors for Choosing Materials
Purpose: How and where will we utilize the material?
The choice of material depends heavily on its intended application. For instance, materials for fuselage construction must be lightweight yet strong. At the same time the engine components need to resist extreme heat and stress.
Production:
How easy is it to manufacture the material? Is it always available and easy to get?
Manufacturing feasibility and material availability are critical. Materials that are difficult to source or process can increase production timelines and costs.
Characteristics:
A material's ability to resist corrosion, response to environmental heat, strength-to-weight ratio, durability, and rigidity all affect its performance under stress.
Researchers evaluate materials for their mechanical and thermal properties to ensure they meet the demanding requirements of aerospace applications.
The Most Common Materials Used in Aerospace
1. Composites
Lightweight and incredibly strong, composites like carbon-fiber-reinforced polymers are widely used in aircraft fuselages, wings, and interiors.
2. Aluminum Alloys
Aluminum alloys offer a great balance of strength, weight, and cost-effectiveness. These are commonly used in structural components such as frames and skin panels.
3. Titanium Alloys
Titanium is valued for its high strength, and corrosion resistance. Its ability to resist extreme temperatures, making it ideal for engine parts and landing gear.
Additional Materials
Other common materials include magnesium alloys, nickel-based superalloys, and advanced ceramics. Each material serves a specific purpose, contributing to the overall performance of the aircraft.
Materials of the Future
1. Metallic Microlattice
These ultra-lightweight materials have exceptional strength. Researchers are developing metallic microlattice for use in structural components, reducing weight without compromising safety.
2. Silicon Carbide
Used in high-performance engines, silicon carbide offers excellent thermal and mechanical properties, enabling it to withstand extreme conditions.
3. Graphene
Graphene is very strong and conducts electricity well. This makes it a great material for future aerospace uses. It can be used for lightweight coatings and advanced sensors.
Additional Future Materials
Other materials under development include aerogels, self-healing polymers, and shape-memory alloys, which could further revolutionize aerospace technology.
The aerospace industry has started using aerogels. Primarily its exceptional thermal insulation properties, low density, and ability to withstand high temperatures, making them ideal for applications like spacecraft insulation. Aerogels are know for its protection against extreme heat during re-entry into the atmosphere.
Aerogel technology is still actively under development. Researchers are continuously working on improving its properties, creating new types of aerogels with different functionalities. And exploring new applications for this versatile material, particularly in areas like energy storage, fire protection, and environmental remediation. These are making it a rapidly evolving field with many ongoing research avenues.
Sustainable Aviation: A Path to Net Zero
With global aviation contributing approximately 2.5% of CO2 emissions, sustainability has become a central focus for the industry. Electric and hybrid-electric propulsion systems are emerging as game changers, especially for regional and short-haul flights. Companies like Airbus and Boeing are investing heavily in developing next-generation aircraft that prioritize environmental performance.
Furthermore, sustainable aviation fuels (SAFs) are gaining traction as a transitional solution. Derived from renewable resources, SAFs can significantly reduce lifecycle greenhouse gas emissions compared to traditional jet fuels. Policies and investments supporting SAF production and adoption will be crucial in meeting the industry's decarbonization goals.
Digital Transformation in Aerospace
Digital technologies are reshaping every facet of aerospace, from design and manufacturing to maintenance and operations. Key developments include:
- Additive Manufacturing (3D Printing) is changing how we build aircraft and spacecraft. It allows for lightweight, complex parts to be made with little waste.
- Artificial Intelligence (AI): AI-powered systems are enhancing predictive maintenance, optimizing flight paths, and improving air traffic management.
- Digital Twins: These virtual copies of real systems let us monitor and simulate in real time. This helps improve efficiency and reduce downtime.
The Rise of Urban Air Mobility (UAM)
Urban Air Mobility (UAM) represents a new frontier in aerospace, promising to revolutionize how people and goods are transported within cities. Electric Vertical Takeoff and Landing (eVTOL) aircraft are at the heart of this movement, combining the convenience of helicopters with the efficiency and sustainability of electric propulsion.
Companies like Joby Aviation and Volocopter are racing to bring eVTOLs to market, with potential applications ranging from passenger transport to emergency medical services. As infrastructure and regulatory frameworks catch up, UAM could become a reality within the next decade.
Space Exploration: Beyond the Final Frontier
Space exploration continues to captivate imaginations and drive technological advancements. A few sources are stating that the privatization of space, led by companies like SpaceX, Blue Origin, and Rocket Lab, has dramatically reduced the cost of launching payloads into orbit. This has opened up opportunities for satellite deployment, space tourism, and even plans for lunar and Martian colonization.
In the future, partnerships between governments and private companies will be key to exploring space. Projects like the Artemis program and plans for a permanent Moon base are on the way.
Conclusion
The aerospace industry stands at the cusp of a transformative era. From revolutionary materials and sustainable aviation to digital innovations and space exploration, the future is bright and full of possibilities. Companies that embrace these changes and invest in cutting-edge technologies will lead the way in shaping the next chapter of aerospace history.
Our Custom Sheet Metal Fabrication for Aerospace
At the heart of these advancements lies precision manufacturing, where materials are shaped and engineered to exacting specifications. We takes pride in offering Custom Sheet Metal Fabrication services that are meticulously tailored to meet the standards of the aerospace industry. This sector is known for its stringent requirements regarding safety, performance, and reliability. And we are committed to delivering solutions that not only meet but exceed these expectations.
Our aerospace metal fabrication services encompass a wide range of capabilities. Which allowing us to produce lightweight components that are essential for enhancing fuel efficiency and overall aircraft performance. We understand that in aerospace applications, every ounce counts, and our expertise in working with advanced fabrication materials ensures that we can create parts that are both lightweight and robust.
Corrosion resistance is another critical factor in aerospace design, as components are often exposed to harsh environmental conditions. We utilize advanced techniques and high-quality materials to manufacture parts that withstand corrosion, thereby extending their lifespan and maintaining the integrity of the aircraft.
Moreover, our team is skilled in developing complex, high-performance designs that are often required in modern aerospace applications. We leverage cutting-edge technology and innovative design practices to create intricate geometries and sophisticated assemblies that fulfill the unique demands of our clients. Our proficiency in this area ensures that we can tackle even the most challenging projects, delivering precision-engineered solutions that align with the latest advancements in aerospace technology.
In addition to our current capabilities, we are also focused on future materials and processes that will shape the aerospace industry. Our commitment to research and development allows us to stay ahead of the curve, ensuring that we can adapt to emerging trends and technologies. This forward-thinking approach guarantees that the sheet metal fabrication materials we work with will reach their maximum potential in aerospace applications, paving the way for innovations that enhance performance, safety, and efficiency.
In summary, Our Custom Sheet Metal Fabrication services are designed with the aerospace industry's demanding standards in mind. Our dedication to quality, innovation, and performance ensures that we provide our clients with the highest level of service and the most advanced solutions available in the market today.
Work with us to bring your aerospace ideas to life. Contact us to learn more about our custom sheet metal fabrication skills!
What innovations are you most excited about? Share your ideas with us or ask for expert's help.
Email us at info@hlhsheetmetal.com !