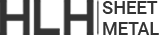
- E-mail: info@hlhsheetmetal.com
- Tel: +86-189-2523-3140
- Room 202, Building 1, No. 1, Datang Hongfa Street, Dalingshan, Dongguan, Guangdong, China 523835
SHEET METAL FABRICATION
INDUSTRIES
The aerospace industry is on the cusp of a manufacturing revolution. At the heart of this transformation is 3D printing, also known as additive manufacturing.
This technology is reshaping how aircraft components are designed and produced. It's enabling unprecedented levels of precision, customization, and efficiency in aerospace manufacturing.
But the story doesn't end with 3D printing alone. Hybrid manufacturing, which combines traditional methods with 3D printing, is also gaining traction. This approach leverages the strengths of both techniques, offering a promising future for aerospace sheet metal fabrication.
In this article, we'll delve into the world of 3D printing and hybrid manufacturing in aerospace. We'll explore their advantages, the materials used, and the role of artificial intelligence in optimizing these processes.
Whether you're a start-up founder, an automotive design engineer, or a product development manager, this comprehensive guide will help you understand and navigate these advanced manufacturing techniques. Welcome to the future of aerospace manufacturing.
Over the past decade, 3D printing has steadily integrated into aerospace manufacturing processes. Initially used for prototyping, it now plays a vital role in producing final parts. This transition from prototype to production marks a significant evolution in manufacturing capabilities.
A major advantage is the ability to create complex geometries that were previously unattainable. Traditional methods often struggled with intricate shapes, but 3D printing offers a solution. This capacity for complexity allows engineers to design parts with superior performance features.
Moreover, the aerospace industry values precision and weight reduction. 3D printing excels in both, providing high precision while using lighter materials. Consequently, components not only perform better but also contribute to fuel efficiency and reduced emissions.
The adoption of 3D printing also encourages innovation in supply chain management. Digital blueprints enable on-demand production, minimizing inventory costs and enhancing operational efficiency. This flexibility fundamentally alters how companies approach manufacturing logistics.
As 3D printing techniques advance, they continue to reshape aerospace manufacturing. The industry is embracing this technology as an essential tool for growth, efficiency, and innovation. This evolution underscores the transformative power of 3D printing in aerospace engineering.
3D printing offers numerous advantages for the aerospace industry. These benefits shape the way designers create and manufacturers produce components.
One key advantage is the precision that 3D printing provides. Traditional manufacturing often involves multiple steps, each introducing potential errors. In contrast, 3D printing builds parts layer by layer, maintaining high fidelity to the design.
Another advantage is the speed of rapid prototyping. Aerospace companies can quickly iterate designs and test new ideas. This capability accelerates development cycles, leading to faster innovation. Reduced time-to-market for new technologies provides a competitive edge.
Customization is also a significant benefit of 3D printing. The aerospace sector can now create bespoke parts tailored to specific applications. On-demand manufacturing further enhances this flexibility, allowing companies to produce exactly what they need, when they need it.
A focus on sustainability drives 3D printing's adoption as well. The additive process minimizes material waste compared to subtractive techniques. By optimizing material use, companies reduce costs and environmental impact.
Key advantages include:
These benefits demonstrate why 3D printing is increasingly favored in aerospace manufacturing. As technology advances, its role will likely expand further.
3D printing excels in creating intricate geometries. This precision is crucial for aerospace applications that demand exact specifications. Complex designs improve performance, weight distribution, and efficiency.
In addition to complexity, 3D printing ensures parts are consistent and reliable. The process precisely forms each layer, reducing defects. This reliability is essential for safety-critical aerospace components.
Rapid prototyping with 3D printing accelerates the design phase. Engineers can test multiple iterations swiftly without lengthy delays. This fast-paced approach allows for quick adjustments and optimizations.
In aerospace, rapid prototyping is invaluable. It cuts down development time, ensuring innovations reach the market faster. This speed is a critical factor in staying ahead of competitors and meeting evolving demands.
3D printing allows for high levels of customization. Aerospace manufacturers can produce unique parts tailored to specific needs. This flexibility supports more innovative designs and solutions.
On-demand manufacturing reduces the need for extensive inventories. Companies can print parts as required, optimizing resources and reducing waste. This approach streamlines operations and reduces excess production.
Sustainability is a significant concern for the aerospace industry. 3D printing offers greener manufacturing by reducing material waste. Traditional methods often leave behind excess materials, unlike the additive nature of 3D printing.
Material efficiency also translates to cost savings. Using just the necessary amount of material lowers production costs. It also aligns with environmental goals, supporting sustainable industry practices.
(image source: Science Direct)
Hybrid manufacturing integrates traditional methods with 3D printing, offering a comprehensive solution. This approach leverages the strengths of both techniques to enhance aerospace fabrication. In doing so, it enables the production of complex components that were previously challenging to achieve.
One significant advantage of hybrid manufacturing is the ability to optimize production processes. Traditional methods provide robust, high-volume manufacturing capabilities. When combined with 3D printing, manufacturers can achieve intricate details and customization within mass production.
This blend enhances material properties and surface finishes by allowing adjustments post-3D printing. You can apply traditional finishing processes to 3D printed parts, which improves their quality and functionality. This integration leads to superior products that meet stringent aerospace standards.
Moreover, hybrid metal fabrication and hybrid manufacturing reduces costs and lead times. By combining efficient traditional techniques with innovative 3D printing, companies can achieve better results. This synergy fosters greater innovation, offering a competitive edge in the aerospace industry.
While 3D printing has many advantages, it also has limitations. These include slower production speeds and potential material constraints. Hybrid manufacturing addresses these by enhancing 3D printed parts with traditional techniques.
This combination allows for the use of diverse materials and finishes, improving final part quality. As a result, aerospace manufacturers achieve more reliable and versatile components than standalone methods could provide.
Talk to our experts. Our qualified engineers are always happy to answer your questions.
Numerous aerospace companies have successfully implemented hybrid manufacturing. These case studies illustrate how combining traditional and additive methods leads to innovation. For instance, some manufacturers use 3D printing for engine components, adding precise, small-scale features.
In another example, a company developing satellite parts improved part performance through hybrid processes. By leveraging both 3D printing and traditional machining, they achieved optimal material characteristics. This dual approach allowed for enhanced durability and reduced component weight.
These success stories highlight the transformative power of hybrid manufacturing. In blending the old with the new, aerospace companies unlock new potentials. Such initiatives set the stage for future advancements, securing a more innovative and efficient industry.
In aerospace manufacturing, selecting the right materials is crucial. 3D printing has expanded the range of materials available for complex aerospace applications. These materials meet strict performance and safety requirements, enhancing the functionality of aerospace components.
A key benefit is the ability to utilize materials with specific properties tailored to design needs. The aerospace industry benefits greatly from high-performance materials. These materials ensure that components meet rigorous standards for strength, durability, and weight.
In recent years, the use of high-performance polymers and metals in 3D printing has grown. Polymers like PEEK and PEI offer high resistance to heat and chemicals. These characteristics make them ideal for aircraft interiors and other critical components.
Manufacturers frequently use metals, such as titanium and aluminum alloys, in 3D printing. People prize them for their superior strength-to-weight ratios and corrosion resistance. These properties make them perfect for engine parts and structural components.
Advancements in material science continually enhance 3D printing capabilities. Researchers are developing new composite materials to meet evolving aerospace demands. These innovations aim to combine the best features of existing materials.
Emerging materials include ceramic-based composites and carbon-fiber-reinforced polymers. These offer enhanced mechanical properties and thermal stability. As innovations continue, they pave the way for more efficient and robust aerospace applications.
Certification and standardization are fundamental in aerospace manufacturing, especially with 3D printing. Each 3D printed component must meet strict safety regulations. This ensures reliability in flight-critical situations.
The process of certifying 3D printed parts involves rigorous testing. It assesses the mechanical properties and durability of materials. Only when these parts meet aerospace standards can manufacturers use them in aircraft manufacturing.
In addition to safety, standardization promotes quality consistency across the industry. Aerospace companies must work with regulatory bodies to establish these standards. This collaborative effort ensures that 3D printing technologies evolve safely and responsibly, supporting broader adoption in aerospace applications.
Artificial Intelligence (AI) and Machine Learning (ML) are reshaping 3D printing processes in aerospace. These technologies analyze vast amounts of data. This analysis enhances precision and reduces errors in manufacturing.
AI models predict how different materials behave during printing. By doing so, they optimize the setup for each print. This leads to improved quality and lower material wastage.
Moreover, ML algorithms continually learn from printing processes. This learning enables adaptive control systems that refine parameters in real-time. As a result, 3D printing becomes faster and more efficient, thus benefiting aerospace manufacturing greatly.
The introduction of 3D printing is transforming aerospace supply chains. Traditional manufacturing relies on extensive and complex logistics. In contrast, 3D printing enables localized production, reducing dependency on global supply networks.
This technology allows for on-demand manufacturing, which minimizes inventory costs. Aerospace companies can produce parts as needed, significantly shortening lead times. As a result, they can be more agile and responsive to market demands.
Moreover, digital inventories replace physical stockpiles. This shift not only improves supply chain resilience but also enables rapid iteration of designs. Aerospace manufacturers enjoy increased flexibility, adapting swiftly to new challenges and opportunities.
Outsourcing to China for manufacturing is a popular choice in many industries. However, 3D printing in aerospace demands careful consideration. While China offers cost-effective solutions, quality and compliance are critical in aerospace.
China has invested in 3D printing capabilities, making it a competitive option. The country's infrastructure supports rapid production and scaling. Yet, the aerospace sector requires stringent standards and tight quality control measures.
Before outsourcing, businesses must weigh several factors. Ensuring adherence to international certifications and standards is paramount. Moreover, intellectual property protection and supply chain security need robust strategies. Ultimately, the decision depends on aligning business objectives with these considerations, ensuring high-quality outcomes.
The future of 3D printing in aerospace manufacturing is rich with promise. This technology transforms the design and manufacturing processes of aircraft. Each year, we see innovations pushing the boundaries of what's possible.
One significant impact is on the production timeline. 3D printing slashes the lead time from conception to execution. This rapid production cycle means quicker market entry, which is vital in a competitive industry.
Additionally, it supports the creation of more advanced, lightweight components. The aerospace industry constantly seeks to enhance performance and efficiency.
The integration of smart technologies is another exciting development. Artificial intelligence (AI) and machine learning refine the printing process. They ensure greater precision and reduce material wastage. As these technologies improve, 3D printing becomes even more powerful and accurate.
We cannot overlook the environmental impact. The push for sustainable manufacturing is strong. 3D printing contributes to this goal by minimizing waste and optimizing materials.
This aligns well with the aerospace industry's move towards greener practices. Together, these factors make a compelling case for the continued adoption and evolution of 3D printing in aerospace.
Technological advancements in 3D printing promise substantial growth in aerospace. Techniques like multi-material printing enhance part functionality. This leads to components that combine strength with reduced weight.
Additionally, we're witnessing improvements in the speed and precision of printers. Faster machines increase production rates without sacrificing quality.
The growth potential for 3D printing in aerospace is vast. Investments in research and development pave the way for innovations. The increasing complexity and customization of parts could redefine aircraft manufacturing.
As these technologies evolve, they enable the creation of highly specialized, optimized components. The potential for transformative change in the aerospace sector is unprecedented.
Despite its promise, 3D printing faces significant challenges. One critical hurdle is ensuring compliance with stringent aerospace standards. Meeting safety and certification requirements is non-negotiable. Manufacturers must invest in rigorous testing and validation processes.
Another challenge is integrating new technologies into existing systems. Bridging traditional and modern manufacturing practices requires strategic planning. Training a skilled workforce is essential to fully leverage 3D printing's capabilities.
Addressing these challenges ensures that 3D printing can achieve its full potential in aerospace. Solving these issues positions the industry to capitalize on the vast opportunities ahead.
3D printing is reshaping the landscape of aerospace manufacturing. This technology offers numerous benefits, including enhanced speed, customization, and material efficiency. By integrating 3D printing, aerospace companies can achieve unprecedented levels of innovation and competitiveness.
The road ahead holds both challenges and opportunities. Addressing certification and integration issues is crucial for success. However, the potential rewards from reduced production times and environmental impact make 3D printing an invaluable asset.
Using this technology could bring great improvements in aerospace. It may start a new era of better manufacturing.
Talk to our experts. Our qualified engineers are always happy to answer your questions.