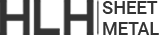
- E-mail: info@hlhsheetmetal.com
- Tel: +86-189-2523-3140
- Room 202, Building 1, No. 1, Datang Hongfa Street, Dalingshan, Dongguan, Guangdong, China 523835
SHEET METAL FABRICATION
INDUSTRIES
The world of manufacturing is evolving. The rise of 3D printing, particularly in metal fabrication, challenges traditional methods.
3D printing, or additive manufacturing, offers a new approach. It builds objects layer by layer, allowing for intricate designs and minimal waste.
But what happens when you combine this innovative technology with traditional metal fabrication techniques? You get a hybrid manufacturing model that leverages the strengths of both worlds.
This article explores this intersection. It delves into the benefits, challenges, and potential of 3D printing in metal fabrication.
No matter who you are, this article will provide useful insights.
Join us as we navigate the exciting landscape where 3D printing meets traditional manufacturing in metal fabrication.
3D printing metal fabrication is redefining manufacturing. By creating parts directly from digital designs, it allows complex geometries that traditional methods struggle to achieve.
Traditional metal fabrication often involves subtractive techniques, like CNC machining, and formative processes, like casting and forging. These are well-established but limited by their nature.
In contrast, 3D printing builds objects layer by layer. This additive method offers substantial design freedom, accommodating intricate internal structures and customizations.
Key components in this innovative process include:
Companies integrating 3D printing with traditional methods are gaining competitive advantages. They achieve faster prototyping and reduced lead times, crucial in industries like automotive and consumer electronics.
Manufacturing has seen a shift in recent years. Traditional methods dominated for decades but are now evolving with technology.
Subtractive manufacturing involves removing material to form the desired shape. It has limitations, such as high waste and design constraints.
(by Yasin Hemmati: https://unsplash.com/@yasinb3da)
The move to additive manufacturing, like 3D printing, changes the process profoundly. It builds parts from the ground up, offering previously impossible design possibilities.
This evolution marks a significant change. With additive manufacturing, designers can focus on optimization and innovation without traditional constraints holding them back.
3D printing provides numerous benefits in metal fabrication. These advantages can transform production lines and boost efficiency.
First, 3D printing reduces waste. Traditional methods often produce excess material, but additive manufacturing uses only what is necessary.
Additionally, customization is a major advantage. You can tailor products to specific needs without extensive retooling, which benefits small batch production.
3D printing also supports rapid prototyping. Developers can iterate designs swiftly, shortening the product development cycle.
Some key benefits include:
The implications are clear: adopting 3D printing for metal fabrication can lead to significant time and cost savings. Embracing this technology can help industries respond more quickly to market demands and drive innovation forward.
The choice of metal is crucial in 3D printing and directly impacts the final product's performance. Not all metals are suitable for 3D printing, but advancements have expanded the range significantly.
Each metal type has unique properties influencing strength, durability, and thermal resistance. These characteristics define their applicability for various industries.
When choosing materials for 3D printing, think about the mechanical properties you need. Also, consider the environmental conditions the part will encounter.
Some widely used metals include:
The variety in 3D printing metal materials allows industries to tailor parts to meet specific performance standards. Understanding the properties of each metal ensures the creation of components that deliver optimal performance for their intended use.
3D printing has embraced metals that offer advantageous properties for specific applications. Stainless steel remains a top choice due to its robust nature and resistance to rust, making it suitable for industrial and consumer products.
Titanium is prized for its high strength-to-weight ratio. It’s frequently used in aerospace for parts needing lightweight durability. Moreover, titanium's biocompatibility makes it ideal for medical implants.
Aluminum alloys, known for their lightness and flexibility, are popular in automotive design. They contribute to fuel efficiency without sacrificing performance.
Understanding these materials' unique benefits assists companies in optimizing their use. Whether for structural components or intricate designs, each metal's features present opportunities for innovative solutions in manufacturing.
When planning 3D printed metal components, several factors influence their effectiveness. Consider thermal properties, as they affect performance under various temperature conditions.
Additionally, assess mechanical properties like tensile strength to ensure the material withstands operational stresses. This is crucial for safety-critical applications in industries like automotive and aerospace.
The cost and availability of materials also impact the selection process. Balancing these with performance requirements ensures both efficiency and feasibility.
Prioritizing these considerations can lead to durable, high-performance components that meet demanding specifications. As technology evolves, ongoing material research will continue enhancing the scope of 3D printing applications in metal fabrication.
Advancements in 3D printing technology are revolutionizing aerospace manufacturing. This innovative process is rapidly becoming a cornerstone for driving growth, boosting efficiency, and fueling breakthrough innovations. Its widespread adoption not only streamlines production but also redefines design possibilities, highlighting the game-changing role of 3D printing in aerospace engineering.
The hybrid manufacturing model leverages both 3D printing and traditional techniques. This approach addresses various manufacturing challenges and highlights the strengths of each process.
Traditional methods, like CNC machining and casting, offer precision and material selection flexibility. However, they can be costly and limiting in terms of design complexity.
On the other hand, 3D printing excels in creating complex geometries and reducing waste. It supports rapid prototyping and customized production, enabling innovation and quick iterations.
Combining these methods in a hybrid model allows businesses to benefit from:
This model enables the creation of more complex and precise parts, optimizing the manufacturing process. The synergy between 3D printing and traditional techniques fosters a competitive edge for companies aiming to push boundaries in product development.
Talk to our experts. Our qualified engineers are always happy to answer your questions.
Automotive and electronics sectors are pioneers in adopting 3D printing alongside traditional methods. This hybrid approach has led to notable successes in both industries.
In the automotive industry, companies like Ford have integrated 3D printing for rapid prototyping. This has significantly shortened design cycles and allowed for more complex, aerodynamic shapes in vehicles.
Electronics manufacturers have embraced 3D printing to create lightweight and intricate components that improve device performance. For instance, companies use it for heat sinks and internal frameworks in consumer electronics.
These success stories reflect the potential of hybrid manufacturing. By optimizing design and production processes, companies achieve greater product innovation and efficiency.
This blend of technologies is a testament to its ability to meet modern manufacturing demands. As industries continue to explore this model, they uncover new opportunities for growth and advancement.
Adopting a hybrid manufacturing model involves challenges, particularly cost and expertise. The initial investment in technology and training can be substantial.
For startups, this financial barrier might seem daunting. However, considering the long-term benefits and scalability can justify these costs.
Another challenge is the need for specialized expertise in both 3D printing and traditional manufacturing. Hiring skilled professionals and investing in ongoing training are crucial to success.
Collaboration with established manufacturers such as HLH Sheet Metal China can also mitigate these challenges. By sharing resources and knowledge, companies can access the benefits of hybrid manufacturing without bearing all the costs alone.
Ultimately, the commitment to overcoming these hurdles can position businesses for significant competitive advantages. As they integrate advanced techniques, they not only improve their manufacturing capabilities but also strengthen their market position.
China plays a pivotal role in the global manufacturing landscape. Its influence in integrating 3D printing into metal fabrication is profound. This integration has significant global implications.
The country's manufacturing infrastructure is vast, which accelerates the adoption of new technologies. 3D printing aligns well with China's goals of innovation and efficiency. As a result, the synergy between traditional and additive manufacturing is encouraged.
Globally, China's advancements in 3D printing impact supply chains and production capabilities. It enables faster, more flexible manufacturing processes. Companies worldwide benefit from reduced costs and improved production timelines, thanks to China's commitment to pushing these technologies forward.
In China, the relationship between manufacturing and 3D printing is mutually beneficial. This partnership fosters rapid technological advancements. It enhances capabilities in metal fabrication, allowing for greater production efficiencies.
Chinese custom parts manufacturers are quick to adopt and innovate in 3D printing. They use this technology to create complex, high-precision metal parts. This adaptability gives them a competitive advantage in the global market.
Moreover, China's strategic investments in 3D printing research and development have paid off. By supporting open collaboration and sharing expertise, they've accelerated progress and established new industry standards.
Overall, the integration of 3D printing within Chinese manufacturing strengthens the country's position as a leader. It also influences global manufacturing practices, driving a new era of efficiency and innovation across industries.
The future of 3D printing in metal fabrication looks promising, with ongoing technological breakthroughs. Innovations in materials and printing techniques are set to transform manufacturing further. These advancements will lead to faster production and higher-quality outcomes.
As technology evolves, industries must embrace these changes. Companies that integrate 3D printing into their operations can expect enhanced flexibility and reduced costs. This adoption can revolutionize supply chains and create new business models.
Moreover, the potential for mass customization and on-demand production is immense. Businesses will become more agile, catering to niche markets and specific customer needs. Overall, these advancements will redefine industry standards and encourage widespread adoption.
Successfully implementing 3D printing technology requires a robust education and training framework. Workers must learn new skills to operate and maintain advanced equipment. This upskilling is vital for maximizing the benefits of 3D printing.
Collaboration between educational institutions and industry players is essential. By fostering partnerships, stakeholders can develop tailored training programs. These initiatives will prepare a skilled workforce ready to tackle future challenges.
In addition, open collaboration between companies promotes innovation. Sharing knowledge and expertise will accelerate technological advancements. Together, these efforts ensure that the industry remains competitive and poised for future success.
3D printing has undeniably reshaped metal fabrication. By merging with traditional methods, it offers unmatched benefits like customization and reduced waste. This hybrid approach bridges gaps and enhances manufacturing efficiency.
As industries evolve, 3D printing will continue to be a catalyst for change. It empowers businesses to innovate swiftly and meet diverse market demands. The future beckons a world where design freedom and manufacturing flexibility reign supreme. This transformation, driven by 3D printing, solidifies its role as an indispensable tool in modern metal fabrication.
Talk to our experts. Our qualified engineers are always happy to answer your questions.