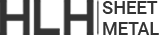
- E-mail: info@hlhsheetmetal.com
- Tel: +86-189-2523-3140
- Room 202, Building 1, No. 1, Datang Hongfa Street, Dalingshan, Dongguan, Guangdong, China 523835
SHEET METAL FABRICATION
INDUSTRIES
The sheet metal forming process is a crucial aspect of manufacturing that involves shaping metal sheets into desired forms. This process is widely used across various industries, including automotive, aerospace, and construction, due to its versatility and efficiency. In this article, we will explore the different methods of sheet metal forming, the advantages of using this process, and its applications in modern manufacturing.
Sheet metal forming refers to the techniques used to manipulate flat metal sheets into specific shapes and sizes. This process can involve bending, stretching, and cutting the metal to achieve the desired geometry. The primary goal is to create components that meet precise specifications while maintaining the integrity and strength of the material.
This is one of the most common sheet metal forming processes. It involves applying force to the metal sheet to create a bend along a straight line. Bending can be performed using various tools, including press brakes and folding machines.
In this process, a flat sheet metal is transformed into a three-dimensional shape by being drawn into a die. This method is often used to create parts like automotive body panels and kitchen sinks.
Stretch forming involves stretching the metal sheet over a form or die to achieve a specific shape. This technique is commonly used for creating large, complex shapes, such as aircraft wings manufacturing.
This continuous process involves feeding a metal sheet through a series of rollers that gradually shape it into the desired profile. Roll forming is ideal for producing long lengths of uniform cross-sections, such as metal channels and rails.
While primarily a cutting process, laser cutting can also be integrated into the sheet metal forming process. It allows for precise cuts and intricate designs, making it suitable for complex components.
Sheet metal forming processes are generally more economical than other manufacturing methods, especially for high-volume production.
This process minimizes waste by utilizing the entire sheet of metal, making it an environmentally friendly option.
Sheet metal forming can accommodate a wide range of materials, including aluminum, steel, and copper, allowing manufacturers to choose the best material for their needs.
Components produced through sheet metal forming often exhibit high strength-to-weight ratios
The applications of sheet metal forming are vast and varied, making it an essential process in modern manufacturing. Industries such as automotive rely heavily on sheet metal processes to produce components like chassis, body panels, and brackets. The ability to form steel sheets into complex shapes allows manufacturers to create lightweight yet strong parts that enhance vehicle performance and fuel efficiency.
In the aerospace sector, sheet metal forming is crucial for producing aircraft components, including fuselage sections and wing structures. The precision and strength of formed metal sheets ensure that these parts can withstand the extreme conditions of flight. Additionally, the versatility of sheet metal manufacturing processes allows for the use of different materials, such as aluminum and titanium, which are favored for their lightweight properties.
The construction industry also benefits from sheet metal forming, as it is used to create roofing, siding, and structural components. The durability and resistance to corrosion of formed metal sheets make them ideal for various building applications. Furthermore, the sheet metal forming process can be tailored to meet specific design requirements, allowing architects and builders to achieve innovative designs.
Talk to our experts. Our qualified engineers are always happy to answer your questions.
As technology advances, so do the methods and techniques used in sheet metal forming. Innovations such as computer numerical control (CNC) machining and advanced robotics have significantly improved the precision and efficiency of the sheet metal manufacturing process. These technologies enable manufacturers to produce complex geometries with minimal human intervention, reducing the risk of errors and increasing production speed.
Moreover, the integration of automation in sheet metal forming processes has led to enhanced productivity and reduced labor costs. Automated systems can handle repetitive tasks, allowing skilled workers to focus on more complex operations that require human expertise. This shift not only improves efficiency but also contributes to a safer working environment.
Sourcing custom sheet metal parts requires careful consideration of factors like cost, quality, lead time, and technical expertise. Options include:
When choosing a supplier, prioritize those with certifications (e.g., ISO 9001, IATF 16949) and proven expertise in your industry. For high-volume projects, overseas manufacturers often provide competitive pricing without compromising quality.
China remains a global leader in sheet metal manufacturing due to:
While concerns about quality and communication persist, reputable Chinese manufacturers adhere to international standards and employ English-speaking teams to streamline collaboration.
HLH Sheet Metal is a China-based manufacturer specializing in precision sheet metal fabrication. Their services include:
HLH Sheet Metal combines cost-effective manufacturing with stringent quality control, ensuring parts meet global standards like ISO 9001 and RoHS.
By partnering with HLH Sheet Metal, businesses reduce lead times by up to 40% while maintaining precision and cost efficiency.
Talk to our experts. Our qualified engineers are always happy to answer your questions.
The sheet metal forming process demands technical expertise and reliable partnerships. While local suppliers offer speed, global manufacturers like HLH Sheet Metal provide unmatched scalability and cost savings. By leveraging China’s manufacturing ecosystem and HLH Sheet Metal’s capabilities, businesses can achieve a competitive edge in product quality and time-to-market.
Sheet metal forming remains indispensable in modern manufacturing, driven by innovations in automation and material science. Whether sourcing locally or overseas, aligning with certified suppliers like HLH Sheet Metal ensures access to advanced technologies, cost efficiency, and consistent quality. As industries continue to evolve, strategic partnerships with experienced fabricators will be key to meeting tomorrow’s design and production challenges.
In conclusion, the sheet metal forming process is a vital component of modern manufacturing, offering numerous advantages such as cost-effectiveness, material efficiency, and versatility. With its wide range of applications across various industries, including automotive, aerospace, and construction, sheet metal forming continues to evolve with technological advancements. By understanding the different methods and benefits of this process, manufacturers can leverage sheet metal forming to create high-quality components that meet the demands of today's market.