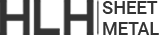
- E-mail: info@hlhsheetmetal.com
- Tel: +86-189-2523-3140
- Room 202, Building 1, No. 1, Datang Hongfa Street, Dalingshan, Dongguan, Guangdong, China 523835
SHEET METAL FABRICATION
INDUSTRIES
Rapid prototyping is the starting gate for improving product design, with each iteration refining parts to ensure fit, form, and function. Yet as complexity grows, teams must also manage supply-chain volatility and diversify sourcing to maintain continuity in development. The following ten focus areas—from material selection to standardized documentation—provide a structured roadmap to optimize your prototype-to-production workflow.
Our 2025 Prototyping Checklist brings together industry-proven best practices—spanning material selection, DFM, cutting-edge prototyping technologies, quality control, sustainability, supply-chain resilience, rapid iteration, risk mitigation, cross-functional alignment, and documentation standards—to help product teams hit every milestone with confidence
Choosing the right alloy upfront prevents downstream headaches. Leverage little-known material selection tips — such as matching tensile strength and work-hardening characteristics to part geometry—to keep your project on budget and on schedule. Consult material libraries early, and validate corrosion resistance and surface finish requirements during the first prototype run.
Incorporate DFM guidelines from day one to reduce tear-out and springback. Maintain hole-to-edge clearances of at least three times material thickness and use bend radii ≥ material thickness to avoid cracking and dimensional drift. Employ automated design-analysis tools to flag problematic features and accelerate feedback loops.
Assess which rapid-prototype process delivers the best ROI for your application. From AI-driven CNC to multi-axis machining and additive hybrid workflows, choose technologies that hit tolerances and cycle-time targets without overinvesting in tooling. Early alignment between design intent and manufacturing capabilities minimizes surprises in later stages.
Embed quality gates at critical junctures. Define inspection points—from initial dimensional audits to material certification checks—to catch deviations before they cascade. For regulated sectors like medical devices, follow on-demand manufacturing guides to ensure compliance with ISO 13485 protocols.
Adopt ISO 14001–aligned processes to systematically reduce waste and resource consumption, driving both environmental and cost benefits. Regularly review life-cycle impacts—from raw-material sourcing through end-of-life—to continuously improve your environmental performance.
Mitigate disruptions by diversifying your supplier base and embracing nearshoring where feasible. Develop a clear disruption-response checklist—mapping exposure levels, defining backup suppliers, and establishing rapid communication channels—to restore operations swiftly when crises strike.
Accelerate design validation with low-volume runs and hybrid CNC/additive prototyping. Quick-turn services deliver testable parts in days, enabling early form-fit-function reviews without committing to large batches. Use data from each iteration to refine CAD models and tooling parameters, shortening overall development cycles.
Implement predictive-maintenance programs powered by digital twins to minimize unplanned downtime and extend equipment life. Real-time analytics from virtual replicas of your shop-floor assets enable proactive responses to emerging issues, safeguarding both prototyping schedules and production quality.
Foster tight alignment between design, engineering, procurement, and quality teams. Use design-thinking workshops and agile sprints to drive shared understanding and rapid decision-making. Maintain a living design system—documenting components, patterns, and process guidelines—to ensure consistency across iterations and stakeholders.
Leverage ready-to-use NPI templates for product definitions, build-readiness checks, and supplier evaluations to streamline handoffs and audits. A standardized New Product Introduction checklist helps capture requirements, risks, and sign-off criteria in one place, reducing misunderstandings and rework.
By systematically addressing these ten areas, you’ll transform your prototyping workflow from a sequence of isolated tasks into an integrated, high-velocity pipeline—maximizing quality, mitigating risk, and accelerating time-to-market.
Talk to our experts. Our qualified engineers are always happy to answer your questions.