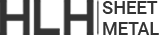
- E-mail: info@hlhsheetmetal.com
- Tel: +86-189-2523-3140
- Room 202, Building 1, No. 1, Datang Hongfa Street, Dalingshan, Dongguan, Guangdong, China 523835
SHEET METAL FABRICATION
INDUSTRIES
The world of manufacturing is constantly evolving. New advancements in materials engineering are pushing the boundaries of what's possible in sheet metal fabrication.
Advanced materials are revolutionizing the industry. They offer unique properties that enhance product design, optimize operations, and improve overall efficiency.
But the integration of these materials is not without challenges. Manufacturers often grapple with sourcing, cost, and regulatory hurdles when adopting these innovative solutions.
This article delves into the world of advanced materials in sheet metal fabrication. It explores their benefits, the obstacles they present, and how to overcome these challenges.
Whether you're an industrial consultant, a medical device designer, or a product development manager, this comprehensive guide will provide valuable insights. It aims to help you navigate the complex landscape of advanced materials in sheet metal fabrication.
Material | Key Properties | Applications |
High-Strength Steel (HSS) | 2–3x stronger than traditional steel, lightweight, and formable. | Automotive frames, crash-resistant components, and energy-efficient structures. |
Aluminum-Lithium Alloys | 7–10% lighter than standard aluminum, enhanced stiffness, and corrosion resistance. | Aerospace fuselages, satellite components, and high-performance automotive parts. |
Titanium Alloys | Exceptional strength-to-weight ratio, biocompatible, and heat-resistant. | Aircraft engines, medical implants, and marine equipment. |
Nickel-Based Superalloys (Inconel, Hastelloy) | Retain strength at temperatures exceeding 1,000°C, oxidation-resistant. | Jet turbines, nuclear reactors, and chemical processing systems. |
Carbon Fiber Reinforced Polymers (CFRP) | 5x lighter than steel, unmatched tensile strength, and fatigue resistance. | Drone frames, luxury car panels, and wind turbine blades. |
Magnesium Alloys | Lightest structural metal (33% lighter than aluminum), vibration-damping. | Laptops, power tools, and automotive transmission casings. |
Shape Memory Alloys (Nitinol) | "Remembers" original shape after deformation, biocompatible. | Stents, robotics actuators, and aerospace couplings. |
Metal Matrix Composites (MMC) | Combines metals (aluminum, titanium) with ceramics/carbon fibers for hybrid strength. | Brake rotors, missile components, and electronic heat sinks. |
Amorphous Metals (Metallic Glass) | Non-crystalline structure, ultra-hard, and corrosion-proof. | Surgical tools, smartphone casings, and industrial coatings. |
Graphene-Enhanced Metals | 200x stronger than steel, electrically conductive, and ultra-light. | Aerospace wiring, battery electrodes, and sensor tech. |
Advanced High-Strength Aluminum (AHSA) | Combines aluminum’s lightness with steel-like durability. | Electric vehicle chassis, aircraft wings, and renewable energy systems. |
Duplex Stainless Steel | Double the strength of standard stainless steel, chloride-resistant. | Desalination plants, offshore oil rigs, and food processing equipment. |
Thermally Stable Ceramic Coatings | Withstand 1,500°C+, reduce friction, and prevent wear. | Engine components, cutting tools, and turbine blades. |
High-Entropy Alloys (HEAs) | Blend 5+ metals for extreme toughness, heat/corrosion resistance. | Spacecraft shielding, deep-sea drilling, and military armor. |
Boron Steel | Ultra-high strength after heat treatment, crash-absorbent. | Car safety cages, armored vehicles, and construction beams. |
These innovations address critical demands for light weighting, sustainability, and extreme-performance across industries like aerospace, automotive, energy, and healthcare. By leveraging advanced materials, manufacturers achieve faster production, longer product lifecycles, and reduced environmental impact.
Sheet metal fabrication has a rich history. It dates back to ancient civilizations using basic tools and techniques to create essential metal components.
Throughout the centuries, the industry has transformed. The introduction of industrialization marked a significant turning point, bringing machinery that enhanced precision and volume.
In today's world, fabrication technology includes computer-aided design (CAD) and computer-aided manufacturing (CAM). These advances allow for intricate designs and streamlined production processes.
These techniques have paved the way for even more advances with new materials.
The evolution of fabrication is a testament to human ingenuity. By embracing innovation, the industry continues to push boundaries and meet ever-increasing demands for complex, high-quality metal products. As materials continue to evolve, so too will the methods of shaping and forming sheet metal, ensuring the industry remains at the forefront of technological advancement.
Talk to our experts. Our qualified engineers are always happy to answer your questions.
Advanced materials in sheet metal fabrication refer to state-of-the-art alloys and composites with improved properties. These materials offer superior strength, flexibility, and corrosion resistance compared to traditional metals. They are designed to meet the demands of modern manufacturing processes.
These materials include a variety of innovations, such as high-strength steel, aluminum alloys, and titanium composites. Each type comes with distinct advantages for specific applications. For instance, titanium is popular in aerospace for its lightweight nature and high strength-to-weight ratio.
In the context of metal fabrication, the adoption of advanced materials allows for the creation of parts that are not only lighter but also more resilient. This enhances product performance and extends the lifespan of the fabricated components. The ability to tailor materials to specific requirements also opens new possibilities in design and engineering, pushing the boundaries of what is possible in industrial applications.
Related Article: Advanced Materials in Aerospace: Revolutionizing Aircraft Design
Using advanced materials in manufacturing provides numerous distinct advantages. These benefits enhance operational efficiency, product durability, and economic viability. As a result, companies gain a competitive edge.
Firstly, advanced materials offer improved strength and lighter weight. This enables the production of durable products without compromising performance. Industries can create more complex designs which are both functional and aesthetically pleasing.
Additionally, these materials contribute to significant cost savings. Their durability reduces the need for frequent replacements, leading to lower maintenance costs. Over time, this results in substantial savings for manufacturers.
Moreover, advanced materials have positive environmental impacts. With lighter and stronger materials, energy consumption decreases in transportation and manufacturing. This is crucial for companies aiming for sustainability.
Lastly, integrating advanced materials increases market adaptability. By quickly responding to consumer demands, manufacturers can introduce new products efficiently. This agility allows firms to lead in rapidly changing industries. Overall, advanced materials significantly boost manufacturing capabilities and outcomes.
Advanced materials play a crucial role in enhancing operational efficiency. They streamline production processes and optimize resource use. This leads to a more agile manufacturing environment.
One way these materials boost efficiency is through reduced downtime. Their durability decreases equipment wear, resulting in fewer production halts. This ensures smoother operations and consistent output.
Moreover, advanced materials support faster manufacturing cycles. Their properties enable quicker processing times, from cutting to shaping. As a result, companies can meet customer demands promptly and increase throughput.
Finally, these materials facilitate automation in manufacturing. Their predictable behavior allows for more reliable integration with advanced machinery. This reduces the need for manual intervention and enhances precision. By leveraging advanced materials, manufacturers significantly improve operational efficiency and maintain a competitive advantage in the market.
Sustainability is a growing priority in sheet metal fabrication. Innovative materials play a pivotal role in this shift. They enable eco-friendly manufacturing practices, reducing environmental impact.
These materials often come from renewable sources, minimizing reliance on non-renewable resources. They enhance recyclability, decreasing waste in the production cycle. This contributes to a circular economy, promoting sustainable development.
Manufacturers benefit from using sustainable materials by lowering energy consumption. These advanced materials often require less energy for processing. Thus, they reduce overall operational costs and carbon footprints.
By integrating innovative materials, companies address sustainability demands effectively. This not only satisfies consumer expectations but also enhances brand reputation. Embracing sustainable materials ensures long-term industry viability and environmental stewardship.
Lightweight materials are changing product design in remarkable ways. They provide designers with new possibilities that were once unimaginable. In industries like aerospace and automotive, reducing weight is crucial.
The use of lightweight materials leads to products that are easier to handle and transport. They enhance fuel efficiency in vehicles, which reduces operational costs. This focus on efficiency can give companies a competitive edge.
Furthermore, lightweight materials allow for intricate designs that prioritize performance without sacrificing strength. Such materials boost durability while maintaining the aesthetic appeal of the product. This balance attracts customers seeking the best of both worlds.
As consumer electronics continue to shrink in size yet grow in capability, lightweight materials become more important. They help in managing thermal loads and improving energy efficiency. By incorporating these materials, designers can push the boundaries of innovation, leading to cutting-edge product offerings.
Selecting materials for medical devices involves meeting strict regulatory standards. The biocompatibility and safety of materials are crucial considerations. Failure to adhere can lead to product recalls and legal issues.
Advanced materials can offer improved performance, but they must be approved by relevant authorities. Materials like titanium and certain polymers are popular for their compliance and effectiveness. These materials combine durability with compatibility, making them ideal for use in medical applications.
Manufacturers must stay updated on changing regulations to ensure compliance. This involves regular audits and adjustments to material choices. Adapting swiftly to regulatory changes can keep product development on schedule.
The selection process is not just about compliance. It also involves optimizing the material for function and performance. By choosing the right materials, medical device designers can create products that are both innovative and safe for consumers.
Related Article: Top Materials Used in Medical Sheet Metal Fabrication - A Comprehensive Guide
Integrating advanced materials into sheet metal fabrication comes with unique challenges. Manufacturers often face difficulties in adapting existing processes to accommodate new material properties. These challenges require innovative solutions and proactive planning.
Material variability is another obstacle. Advanced materials can have different behaviors under stress compared to traditional metals. Predicting how they will respond during fabrication processes such as cutting or bending is crucial. Manufacturers must conduct rigorous testing and simulations to anticipate these responses.
Cost is also a significant concern. Advanced materials can be more expensive, impacting overall project budgets. To mitigate these costs, manufacturers must evaluate long-term savings and performance benefits. Cost-effective strategies, such as bulk purchasing and optimizing resource use, should be explored.
Open communication between designers and fabricators is essential. This collaboration helps identify potential issues early, reducing delays and improving outcomes. By leveraging teamwork and technology, manufacturers can successfully integrate advanced sheet metal materials into their operations, driving innovation and efficiency.
Talk to our experts. Our qualified engineers are always happy to answer your questions.
Aerospace is leading the charge in using advanced materials. Boeing's transition to carbon fiber reinforced polymers in aircraft manufacturing exemplifies this. These materials significantly reduce weight, boosting fuel efficiency without compromising strength.
In the automotive industry, Tesla's use of aluminum alloys for its car bodies is noteworthy. These alloys offer a balance between weight reduction and structural integrity. As a result, Tesla has enhanced vehicle performance and energy efficiency. This innovative approach showcases the impact of advanced materials in product development.
Medical device manufacturers also benefit from advanced materials. For instance, titanium's use in surgical implants has improved biocompatibility and durability. These properties help devices integrate seamlessly with human tissue. Consequently, patient outcomes have improved markedly.
Electronics manufacturers are using advanced materials to their advantage as well. Samsung has incorporated graphene in its battery technology. Graphene significantly increases battery life, allowing devices to charge faster. This advancement underlines how innovative materials can revolutionize consumer electronics.
These case studies demonstrate the diverse applications and benefits of advanced materials in sheet metal fabrication. By exploring and adopting these materials, industries can push the boundaries of innovation and efficiency. The success stories set a precedent for others to follow.
The properties of materials significantly influence fabrication techniques. Strength, flexibility, and thermal conductivity dictate how materials can be processed. Bending and cutting processes must align with the material's characteristics.
For example, metals with high tensile strength require specialized equipment for processing. Conversely, materials with lower melting points allow for more versatile fabrication methods. This diversity in material properties expands the possibilities within manufacturing.
Advanced materials have pushed the boundaries of what techniques can achieve. Innovations like 3D printing accommodate a wide range of material properties. These properties include flexibility and heat resistance, broadening manufacturing capabilities.
Engineers and designers carefully consider material properties during the fabrication process. This selection ensures the desired outcomes in product performance and longevity. A thorough understanding of these properties allows for optimizing manufacturing operations, enhancing both efficiency and quality.
Quality control is vital in sheet metal fabrication. It ensures that the products meet the desired specifications. Rigorous testing of materials before fabrication helps in minimizing defects.
Materials testing involves various methods. These methods assess the mechanical and chemical properties of materials. Accurate testing informs decisions about the fabrication processes.
Advanced materials require sophisticated testing techniques. Non-destructive testing methods are often used. These techniques preserve the integrity of expensive or rare materials.
Quality assurance processes extend beyond initial testing. Continuous monitoring during production is also crucial. This ensures that the final products consistently meet required standards. By adopting robust quality control measures, manufacturers can maintain high levels of precision and reliability.
Digital technologies are transforming metal fabrication. These advancements allow for precise customization of metal parts. Fabricators can now meet specific client needs with ease.
Computer-aided design (CAD) is crucial in this process. CAD software enables detailed and accurate design of custom parts. It allows designers to visualize parts before production begins.
3D modeling further enhances customization. It provides a virtual prototype, reducing the need for physical ones. This step lowers cost and speeds up the design process.
Moreover, digital tools improve communication between designers and fabricators. Real-time data sharing helps ensure that designs are accurately implemented. This synergy leads to efficient and high-quality production outcomes.
China has become a global leader in metal fabrication. Its extensive capabilities support businesses worldwide with custom metal parts. Companies benefit from China's advanced manufacturing technology and skilled workforce.
Cost-effectiveness is a key advantage. Chinese manufacturers offer competitive pricing due to lower labor and production costs. This affordability does not compromise quality or precision.
Moreover, Chinese suppliers are adept at handling large-scale projects. Their capacity to produce high volumes quickly is unmatched. This ensures timely delivery, which is crucial for meeting production deadlines.
Partnering with China also opens doors to a wide range of materials. Chinese manufacturers have access to various innovative and lightweight materials. This broad selection helps companies push the boundaries of design and functionality.
The future of advanced materials in sheet metal fabrication is promising. Research and development continue to accelerate, paving the way for groundbreaking innovations. Industries are set to benefit from these advancements.
Nanotechnology is one area to watch. It offers the potential to create stronger, lighter, and more durable materials. This can revolutionize applications across aerospace, automotive, and electronics industries.
Additionally, smart materials are gaining traction. These materials can adapt to environmental changes, enhancing product functionality. They could lead to innovations in consumer electronics and medical devices.
Sustainability will also play a pivotal role. The integration of eco-friendly materials in manufacturing processes is likely to increase. This aligns with global efforts to reduce environmental impact and promote sustainable practices.
Finding reliable sources for advanced materials requires diligence and strategic planning. Start with extensive market research to identify potential suppliers. Understanding market trends can guide your sourcing decisions effectively.
Building strong relationships with suppliers is crucial. Engage with them regularly to ensure a consistent supply of high-quality materials. Clear communication helps in understanding their capabilities and limitations.
Consider suppliers' certifications and accreditations. These validate their commitment to quality standards and compliance. Prioritize those who demonstrate a track record of excellence.
A checklist can streamline your sourcing process:
• Verify supplier credentials
• Assess material quality through testing
• Request samples for evaluation
• Negotiate favorable terms and conditions
Lastly, attend trade shows and industry conferences. They offer opportunities to network with suppliers and discover new materials. Keeping abreast of industry innovations enhances your sourcing strategy.
The role of advanced materials in sheet metal fabrication is transformative. As technology evolves, these materials redefine what is possible in manufacturing. They allow for more efficient processes and innovative designs.
Adopting these materials means staying competitive in a fast-paced market. Manufacturers and designers who embrace these changes can create superior products. This positions them strongly for future challenges and opportunities.
Ultimately, the evolution of materials engineering leads to more sustainable solutions. By exploring innovative materials, industries can achieve growth and sustainability. The journey into advanced materials sets the pace for the future of fabrication.
Talk to our experts. Our qualified engineers are always happy to answer your questions.