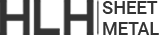
- E-mail: info@hlhsheetmetal.com
- Tel: +86-189-2523-3140
- Room 202, Building 1, No. 1, Datang Hongfa Street, Dalingshan, Dongguan, Guangdong, China 523835
SHEET METAL FABRICATION
INDUSTRIES
The custom sheet metal fabrication industry is undergoing a revolution. This transformation is driven by the integration of artificial intelligence (AI) and automation.
These technologies are enhancing precision and efficiency in remarkable ways. They are reshaping how sheet metal is cut, bent, and assembled into bespoke products.
AI design tools are at the forefront of this change. They assist engineers in optimizing designs for manufacturability and cost-effectiveness.
Automation, on the other hand, reduces human error. It increases production speed, leading to more efficient processes and higher-quality products.
Companies like HLH Sheet Metal are leveraging these advancements to stay competitive. This article aims to shed light on the impact of AI and automation in the custom sheet metal fabrication industry.
Join us as we delve into the benefits, applications, and future of AI in this rapidly evolving field.
Custom sheet metal fabrication has a rich history. Traditionally, it involved skilled craftsmen manually cutting and shaping metal. This process was slow and prone to errors.
As technology advanced, machines began assisting in fabrication. These machines improved speed and accuracy but still required significant human oversight. The industry saw gradual improvements in machinery and processes.
With the advent of computer-aided design (CAD), fabricators gained new capabilities. CAD enabled precise design specifications, reducing material waste and optimizing layouts. This marked a significant shift towards digital solutions.
Today, AI and automation are pushing the boundaries even further. AI metal fabrication is one of the hot topic in the internet world now. These technologies allow for innovative approaches that were unimaginable just a few decades ago. Machine learning and predictive analytics are now key components in the fabrication workflow.
The custom sheet metal industry continues to evolve at a rapid pace. As AI and automation mature, fabricators will likely see unprecedented levels of precision and efficiency. The future holds exciting possibilities, as each technological leap paves the way for new advancements.
AI design tools are transforming custom sheet metal fabrication. They empower engineers to create intricate designs with ease. These tools use algorithms to optimize shapes and patterns.
One major advantage of AI design tools is their ability to enhance manufacturability. This means engineers can now design products that are not only innovative but also practical to produce. These tools analyze designs to ensure they can be fabricated efficiently.
Another benefit of automation in metal fabrication is the reduction of human error. AI can simulate fabrication processes, preventing costly mistakes before they occur. This leads to higher precision in manufacturing, aligning with industry demands.
The capabilities of AI design tools include:
The integration of AI in the design process also supports sustainability. By optimizing material use, AI contributes to eco-friendly manufacturing practices.
Furthermore, AI tools facilitate better collaboration among teams. They allow designers, engineers, and manufacturers to work together seamlessly, ensuring cohesive and efficient production. This holistic approach enhances the entire fabrication process.
As the industry grows, AI design tools will play an increasingly crucial role. They not only promise efficiency and precision but also open new doors for innovation. The potential for creative, efficient, and sustainable designs has never been greater.
AI design tools are revolutionizing how products are designed. With these tools, manufacturability becomes a key focus. Engineers can now tailor designs that align perfectly with fabrication methods.
The design phase is now smarter and more strategic. AI algorithms evaluate every aspect of a proposed design. This ensures that it meets practical fabrication criteria.
Additionally, AI tools identify potential fabrication issues early. This proactive approach saves time and resources, ensuring smoother production. By addressing manufacturability, these tools make design a seamless part of the fabrication process.
AI goes beyond design optimization by predicting material behavior. This predictive capability enhances quality control. Engineers benefit from an accurate understanding of how materials will react during fabrication.
Machine learning models analyze historical data. This analysis reveals patterns and trends in material performance. Engineers can then anticipate challenges and devise solutions before issues arise.
Quality control is significantly improved with AI insights. Real-time data helps maintain product consistency and compliance with standards. The use of predictive analytics not only ensures high-quality outcomes but also fosters continuous improvement in production processes.
Automation is transforming custom sheet metal fabrication. It enhances both efficiency and precision in production. Automated systems reduce reliance on manual labor, speeding up processes significantly.
These systems also ensure greater accuracy. Machines perform repetitive tasks with consistency, reducing variability. This results in uniform products that meet strict specifications.
Furthermore, automation minimizes human error. By handling complex calculations and tasks, machines reduce the chances of mistakes. This leads to better quality control and cost savings.
Automated processes also optimize resource use. They can adjust inputs dynamically, ensuring materials are used efficiently. This not only saves costs but also reduces environmental impact.
Overall, automation represents a crucial advancement in fabrication. It aligns with the industry’s push for smarter, more sustainable practices. As technology evolves, automation’s role will only grow, driving further improvements in productivity and quality.
Robots are integral to modern welding and cutting operations. They perform these tasks with unmatched precision. Robotic systems ensure consistent welds and cuts, crucial for high-quality products.
These machines work tirelessly without fatigue. They can handle complex tasks without compromising on accuracy. This reduces the risk of defects and enhances overall quality.
Moreover, robotic systems boost production speed. They operate continuously, increasing output significantly. As a result, businesses achieve faster turnaround times while maintaining high standards.
Real-time parameter adjustments are a game-changer in fabrication. Automated systems dynamically alter settings to optimize outcomes. This adaptability ensures peak performance at all times.
Sensors collect data continuously during production. This data allows systems to adjust processes instantly. As a result, any deviations are corrected on the fly, ensuring consistent quality.
The ability to make real-time adjustments also enhances efficiency. It minimizes material wastage and reduces errors. By leveraging this capability, manufacturers maintain high standards with minimal intervention.
HLH Sheet Metal is a leader in adopting AI within the fabrication industry. We have transformed operations by integrating advanced technologies. This move has significantly enhanced precision and efficiency.
AI-powered systems have become integral to our workflow. These tools have streamlined design processes, reducing time and labor. The result is more efficient production cycles and superior product quality.
Additionally, AI algorithms help predict potential issues before they arise. This predictive capability minimizes downtime and enhances operational reliability. Through such foresight, HLH Sheet Metal maintains a competitive edge.
Our commitment to innovation extends beyond operational improvements. We are pioneering new applications of AI in fabrication. This positions HLH Sheet Metal as a forward-thinking player in a rapidly changing industry landscape.
Rapid prototyping is one of HLH Sheet Metal’s standout capabilities. AI accelerates the transition from design to tangible products. This speed allows for agile responses to market demands.
Mass customization is another area where AI excels. It enables tailored solutions without the extended timelines traditionally associated with custom orders. Products are quickly adapted to meet unique customer needs.
By harnessing AI, HLH Sheet Metal ensures that high-quality, customized products are delivered swiftly. This flexibility caters to diverse client specifications, reinforcing their market leadership.
Talk to our experts. Our qualified engineers are always happy to answer your questions.
AI technology revolutionizes production speed and waste management in sheet metal fabrication. By implementing AI, manufacturers achieve faster throughput and reduced material waste. This dual benefit enhances profitability and sustainability.
Speed is a critical factor in manufacturing. AI systems optimize the production cycle, reducing delays. This leads to quicker project completion and improved customer satisfaction. As a result, companies are more competitive in fast-paced markets.
In addition to boosting speed, AI excels in minimizing waste. Improved precision in cutting and assembly processes means less material is discarded. This efficiency reduces costs and supports environmentally friendly practices.
AI-driven analytics further aid in waste reduction. These analytics assess historical data to refine processes continually. Through this continuous improvement, the fabrication process becomes leaner and more efficient over time.
The nesting process in fabrication determines how parts fit within raw materials. AI automates this task, enhancing material use. Automation ensures minimal scrap, maximizing material efficiency.
By optimizing part layout, AI reduces wastage significantly. This capability transforms production by lowering material costs. Consequently, businesses see substantial savings over time.
Moreover, automated nesting accelerates production. With AI handling the layout design, the entire process is expedited. Fabricators can thus focus on other critical tasks, increasing overall productivity.
The integration of AI in custom sheet metal fabrication extends to predictive maintenance. AI systems analyze machine data, predicting potential failures before they occur. This proactive approach minimizes unexpected downtime, crucial for maintaining production schedules.
Predictive maintenance not only saves time but also reduces repair costs. By addressing issues early, companies avoid expensive breakdowns. This strategy ensures machines run optimally, extending their lifespan and efficiency.
Safety is another area where AI makes a significant impact. AI monitors the work environment, identifying potential hazards. By predicting unsafe conditions, it helps in preventing accidents, safeguarding workers effectively.
Moreover, AI enhances safety measures through automated compliance checks. Systems can verify that safety protocols are consistently followed. This continuous monitoring ensures a safer fabrication environment, fostering a culture of safety and responsibility within the industry.
The future of AI in custom sheet metal fabrication promises exciting advancements. As technologies develop, the capabilities of AI systems grow exponentially. These innovations drive efficiency and open up new possibilities for the industry.
AI will likely become more integrated, enabling smarter and more responsive fabrication processes. This evolution will support greater customization and flexibility in production. Companies that embrace these changes will likely see substantial competitive advantages.
Interconnected systems and data-driven decision-making are at the core of this transformation. AI's ability to process vast amounts of data in real time enhances operational insights. This shift supports more strategic planning and execution in manufacturing.
Moreover, AI in manufacturing helps meet the growing demands for sustainable practices. By optimizing resources and reducing waste, AI contributes to greener fabrication methods. This aligns with global sustainability goals, appealing to environmentally conscious consumers.
The future holds a landscape where AI and human ingenuity work hand in hand. As AI manages repetitive tasks, human creativity can focus on design and innovation. This synergy could define the next era of custom sheet metal fabrication.
Integrating AI raises important ethical questions. As AI systems automate tasks, there's concern about job displacement. Organizations must balance technological growth with workforce stability.
To address these concerns, industries need to prioritize workforce adaptation. Employees should receive training to work alongside AI systems. This approach ensures a smooth transition, maintaining workforce relevance and expertise.
Moreover, ethical AI use involves transparency and accountability. Businesses should implement AI systems with clear guidelines and oversight. This ensures responsible use that respects both employees and consumers.
Continuous learning is essential for maximizing AI's potential. As AI tools advance, staying updated with new capabilities is crucial. Industries need to invest in ongoing training for their workforce.
Learning environments should evolve as quickly as technology. This allows employees to harness AI's full potential and drive innovation. As a result, businesses can maintain their competitive edge in a rapidly changing market.
The evolution of AI brings new opportunities for innovation. By embracing learning and adaptation, companies can lead in AI integration. This proactive stance ensures long-term success in the dynamic field of custom sheet metal fabrication.
The integration of AI in custom sheet metal fabrication has become more than an option; it's a necessity for staying competitive. Companies that leverage AI technologies see significant gains in precision, efficiency, and overall productivity. As a result, they find themselves at the forefront of innovation.
Adopting AI tools ensures businesses can keep pace with industry demands while also advancing their technological capabilities. With AI, fabricators can produce higher-quality products more quickly and with less waste. This technological edge not only benefits production but also enhances customer satisfaction with superior results.
In conclusion, embracing AI is a strategic move that enables firms to thrive in a challenging market. As technology continues to evolve, those who adapt and innovate will maintain their lead. By investing in AI and continuous learning, companies can secure a strong, sustainable future in custom sheet metal fabrication.
Talk to our experts. Our qualified engineers are always happy to answer your questions.